|
Carbon Fibre Tubes, Composite Manufacture for High Performance - An Introduction
Processes
There are a variety of manufacturing processes applicable to
the production of composite tubes. The choice of process is
influenced by the properties required, quantity, costs, etc.
Pre-Preg Rolling
Layers of material are rolled around a mandrel, by hand or machine,
prior to consolidation and cure.
When hard the outside diameter can be machined if required.
Ideal for smaller quantities and smaller tubes where increased
material costs are less significant.
Pultrusion
A continuous process in which fibres in the form of rovings,
mat or fabric are impregnated with resin and pulled through
a heated die of the required shape, moulding both the inside
and outside diameters.
Uses raw materials in their most basic and lowest cost form,
however large quantities need to be produced to justify the
high tooling and set-up costs
Limited choice of fibre angle.
Filament Winding
After impregnating with resin the fibre is wound onto a mandrel
at the angle required to produce the mechanical properties.
Conventionally tubes produced in this way have a moulded Inside
diameter, the outside diameter can be machined if required,
after curing.
Technology developed by Performance Composites Ltd.
allows us to mould the OUTSIDE diameter rather than
the inside diameter, this also allows shallow fibre
angles (typically down to ± 5°.),
and provides better consolidation/laminate quality. |
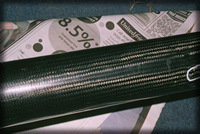 |
This
process is particularly suited to medium to large batch quantities
or larger 'one offs'
|
|
|