|
Carbon Fibre Profiles, Composite Structural Profile System
Introduction
Performance Composites Limited are pleased to introduce a versatile
and economic system for creating composite structures, usefull to
a wide range of industries.
This system is ideal for lightweight, strong and dimensionally stable
components of many types including;
Assembly jigs and fixtures
Inspection equipment
Machine frames
Robotics
The backbone of the system is a range of ‘Standard’ components which
are used individualy or simply cut to the required size and bonded
together to make larger and more sophisticated items.
Although we can make square and rectangular box sections they are
not part of our ‘Standard’ range, fabricated box sections as described
below are more cost effective, and often, structurally more efficient.
The flanges can also be used as attachment points for cable or pipe
runs, etc.
Our system of fabricating ‘box’ section and larger assemblies from
‘I’ beams, angles and pieces of sheet also allows the creation of
tapered, cranked and curved beams without huge tooling costs.
We can supply;
The basic moulded sections in standard lengths for you to cut and
bond together as required.
Kits of parts, ready cut for you to assemble on site.
Complete fabrications to your specifications.
The following pages give some examples of what can be achieved from
some simple sections and some high strength adhesive (normally epoxy
or toughened acrylic). Basic
Sections
The following are ‘STANDARD’ sections,
i.e. produced on simple tooling; the moulded surfaces are shown thicker,
Nominal lengths are 2500 or 3660 mm (12 ft). Other sections and lengths
up to 9000 mm are available as ‘SPECIALS’
The actual size of the section, the fibre type and fibre orientation
are fundamental to satisfactory performance and may vary for each
application, see fibre angle and mechanical property data sheets.
Moulded surfaces are either ‘semi-gloss’ or ‘Peel Ply’
Fabricated Sections
We have created all of the following and many more
Far Left: |
Foam filled ‘I’ beam curved and tapered in both directions.
Used for micrometer body and robot mounted punch & anvil
(end fittings not shown) |
Centre Left: |
Sheet Tapered ‘Box’ (STB), All components from STD range –
just cut the sheet tapered. |
Centre Right: |
Web Tapered ‘Box’ (WTB). ‘I’ beams are SPECIALS but tooling
still low cost. |
|
Note: STB and WTB can be combined in long shallow taper
beams only, too much taper distorts the glue line, weakening
the joint and making assembly difficult. |
Far Right: |
Cranked ‘Box’ made from overlapping ‘I’ beams (one flange
of each beam cut away locally)
Sheets butted at corner and secured with angled butt straps.
Cranks and tapers can be combined |
Standard Sizes ‘I’
Beam
Sizes for A |
1 1/2”
1 3/4”
2”
2 1/4”
2 1/2“
3”
3 1/2“
4”
5”
6” |
38.1
44.5
50.8
57.2
63.5
76.2
88.9
101.6
127.0
152.4 |
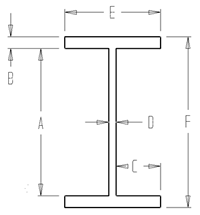 |
Plus many larger sizes
up to 450 mm |
A |
Distance between flanges |
As list above – smaller
sizes are available from 1/4“ (6.35mm) upwards |
B |
Flange Thickness |
Moulded as required –
minimum 0.5 x D plus 1 layer fabric plus UD. |
C |
Flange Cut width |
Machined to suit – Note:
C x 2 + D = E |
D |
Web Thickness |
Moulded to suit application
- Minimum 2 plies fabric @ +/-45 deg. |
E |
Width Overall |
E = 2 x C + D |
F |
Height Overall |
F = 2 x B + A |
Sheet
Thicknesses: |
from 0.25mm upwards. |
Standard sizes: |
1Metre x 1.5m or 1.2m x 1m (nominal) depending on material
manufacturer and 3660 (12ft) x 450 |
Fibre Orientation: |
As required. |
Angle
Thicknesses |
from 0.25mm upwards. |
Standard Sizes: |
100mm (50mm each leg) x 1.2m |
Common angles: |
90, 120, 135, 150 deg. included |
Fibre
Types
Composite Components are constructed from a numerous layers of material,
the fibre type and angle for each layer is arranged to give the overall
mechanical properties required by the application.
The properties listed below are for composites made from UD fibres
@ 60% Vf – See Mechanical properties data sheet. Glass
Fibre
A low cost fibre with good strength, but relatively low stiffness
and high density.
Typically UTS 1.0 Gpa Modulus (Ex) 40 Gpa
Density 1.9 g/cc Aramid Fibre
Tradenamed 'Kevlar' or 'Twaron', aramid fibres have excellent tensile
strengths, nearly twice as stiff as glass fibre, also lighter, but
often needs to be combined with other fibres to achieve acceptable
compressive strengths. Machining can be a problem.
Typically UTS 1.3 Gpa Modulus (Ex) 75 Gpa
Density 1.4 g/cc Carbon Fibre (Standard Grade)
Standard grade carbon fibres have a good combination of strength with
stiffness. With a specific modulus of 92, over 3 times that of metal
(Steel and aluminium are both the same) carbon fibre / epoxy laminates
are finding increasing application.
Typically UTS 1.5 Gpa Modulus (Ex) 130 GPa
Density 1.6 g/cc Carbon Fibre (Special Grades)
Standard grade carbon fibre (T300, HTA, etc) have mechanical properties
with out resin of approx. 3 – 3.5 GPa tensile strength and 230 – 240
GPa Tensile modulus.
Carbon fibre manufacturers are constantly trying to improve the modulus,
and strength, of their fibres. Tensile strengths go up to 7 GPa and
Tensile modulus up to 700 GPa, however it is not possible to get a
fibre with both the above properties, ‘strong’ fibres are not as ‘stiff’
and visa-versa.
There are many grades now available, however increased properties
means higher prices, up to £600.00 per Kg (not for the faint hearted). Fibre Forms
Our products are made from Aerospace type pre-preg materials and/or
by filament winding.
Pre-pregs are fibres that have been Pre-impregnated with the resin/hardener
to form a pliable tacky sheet. They need to be stored cold to prevent
premature reaction of the resin /hardener part.
The main types are UD (Uni-Directional), Woven Fabrics 0/90° and Multiaxials
(frequently of stitched construction)
Components are built up using many layers of fibre, each of which
is suitably arranged to carry the expected loads.
The completed layup is subjected to heat and pressure to give the
final shape.
Components are seldom made with only one fibre direction, as they
would easily split. 0 Degree (Axial)
Resists longitudinal bending and axial tension/compression
In an ‘I’ beam the 0° is placed mainly in the flanges where it can
do most work. +/- 45 Degree
Resists shear and torsion, as seen by the web of an ‘I’ Beam.
Also adds strength around bolt holes. 90 Degree
(Transverse)
Resists internal/external pressure, helps a profile to stay in shape
and adds strength around bolt holes. Quasi-Isotropic.
An equal mix of 0°, 90° +45° and -45° fibres which results in fairly
uniform strength / stiffness in all directions.
With filament winding it is not practical to wind fibres at
exactly 0° or 90°, however components seldom have only one load applied
to them, and will therefore require at least 2 of the above angles
need to be incorporated to carry the combined loads.
Most combined loads can be carried with fibres at an intermediate
angle.
e.g.
For Internal pressure the hoop stress is twice the longitudinal stress
use approx +/-55°.
For External pressure as above but to resist buckling use approx +/-65°.
For Quasi-Isotropic laminate use +/-22.5° & +/-67.5° alternate
layers.
For bending with torsion angles between +/- 5° to +/- 25° are appropriate.
Back to TOP
|
|
|